The manual alignment of shafts requires patience, skill and an eye for detail. In mining, however in which equipment is constantly running and accuracy is paramount, minor errors can become major difficulties.
This is where digital tools are useful. They help make alignment quicker easy, more efficient to do, and more precise. From laser shaft alignment services, wireless sensors and mobile applications the tools can help workers do their work more efficiently, not more difficult.
Mine sites have been able to go through constant vibrations to easy operations through switching to digital processes. Let’s examine the ways these tools can help you get work done with precision and without a lot of guesswork.
Laser Alignment Enhances The Precision
The laser alignment tools do not lie. They provide precise measurements down to fractions of millimeters. It is easy to line up the sensors and run a test, and then the screen will tell you how and where you can adjust.
It’s not a guessing game, and there’s no need to look around. It is crucial to have this precision especially in areas with tight spaces where an inch of offset can throw everything off-balance.
These tools allowed them to correct the issues that they couldn’t even spot by using manual approaches. Precision like this keeps machines working longer and decreases the necessity for repeat adjustments.
Reduces Time For The Task
Its digital aligning tools can speed up the process. The job that used to take days using dial gauges may be completed in a matter of just a few minutes. Sensors stream real-time data to your tablet or handheld device.
The user makes a motion and your screen displays what happens immediately. This means fewer re-dos as well as a smoother flow. The crew can complete their work faster and without having to cut corners.
Particularly in highly pressured environments such as mines where interruptions cost thousands of dollars every minute, even a fraction of one hour can make a huge significant difference.
Improves Record Keepers
Record Keeping instruments keep all alignment information. Every adjustment, every reading or job, is recorded and saved. It makes work in the future much simpler.
The mine I was in made use of this data to show that their alignment system was functioning. Less breakdowns, more equipment longevity, and lower maintenance expenses, all backed up by numbers.
The digital record also assists in audits, safety inspections and arranging maintenance based on actual information, not speculation or memory. This helps keep teams on track and in sync.
Assists In Training New Technicians
Lasers and digital devices don’t just assist experienced mechanics; they also help novice technicians learn more quickly. They learn through visual feedback how to properly align.
They can see immediately what’s wrong and the best way to correct the issue. One instructor I talked to describe the process “alignment with training wheels,” and meant it to be praise.
The tools help crew members feel confident. This builds confidence in the system and cuts short the amount of time needed to create a stable maintenance staff.
Is A Great Choice For Those Who Work In Harsh Conditions.
Environments in mining don’t have a good reputation. There’s dust, cramped space, inadequate lighting and a lot of vibrating. However, modern digital shaft replacement devices have been designed to last.
They’re dust and shockproof and some are even wireless. It means no more lugging around with heavy gear or having to read the dials by using an illuminated flashlight inside your mouth.
An alignment technician I know has his Bluetooth laser set on his belt — it’s so portable. If tools are simple to use and carry around aligning checks are performed more frequently.
Final Thoughts
The digital aligners take all the task of guesswork. They’re more efficient, accurate and much easier to employ in the harsh field of mining.
The crews can complete jobs faster they can spot issues earlier and maintain a higher-quality record of their work. Team members who are new learn faster and experienced technicians waste more time doing repetitive work.
If you’re still operating an old-fashioned method perhaps it’s an ideal time to consider giving digital tools the chance. There’s a good chance you’ll be wondering the reason you didn’t change sooner.
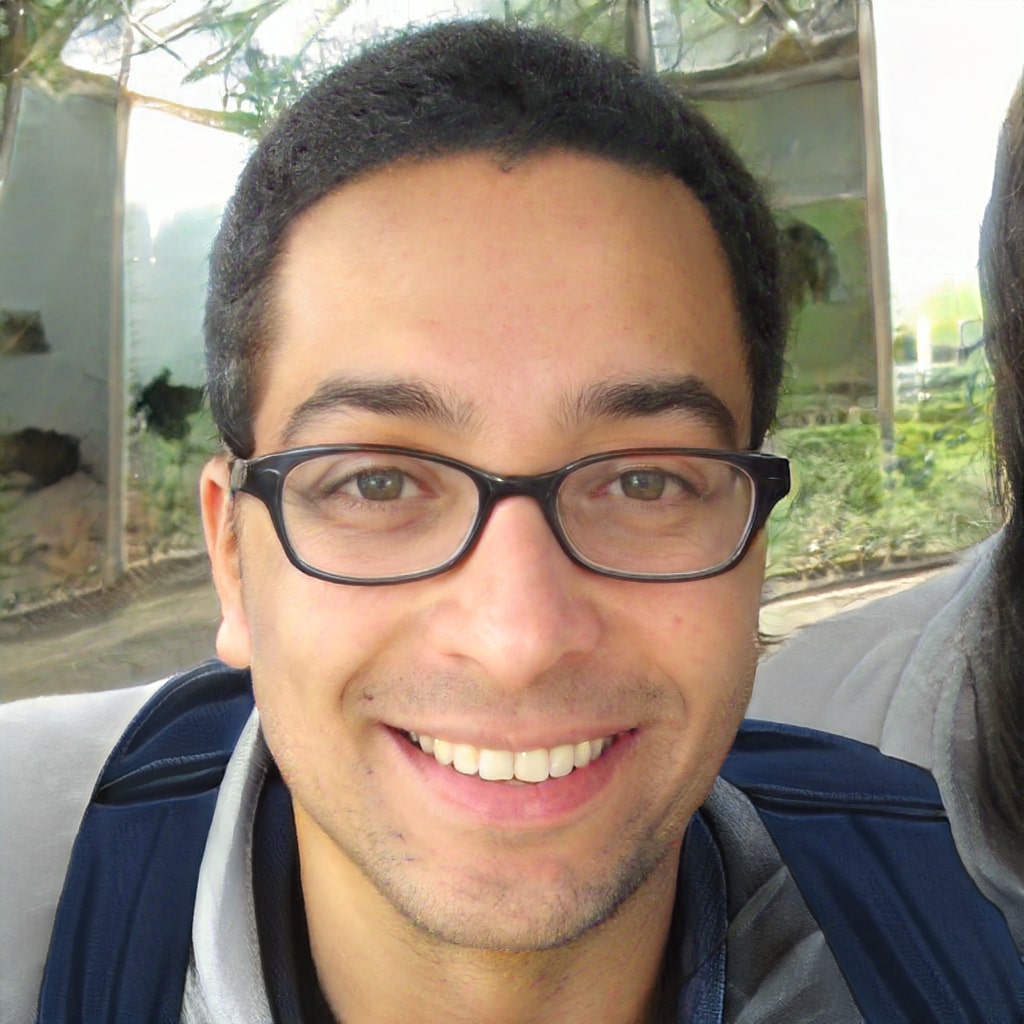